Case Study – Application Development
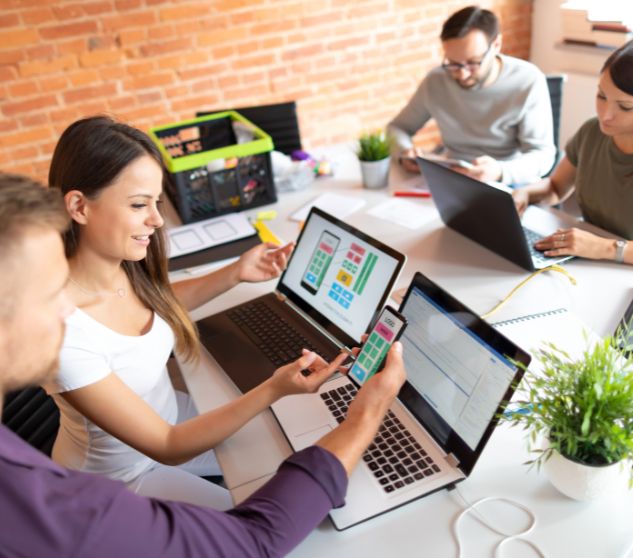
Introduction
H.M.A. Enterprises, a leading player in industrial equipment manufacturing, needed a powerful application solution to streamline its manufacturing and inventory management processes. Known for producing high-quality machinery, H.M.A. faced increasing demand and complex production workflows that required digital transformation. H.M.A. partnered with Datazen Technologies to design and implement a custom application that could unify operations, optimize productivity, and enhance their supply chain and inventory management.
Challenges Faced
H.M.A. Enterprises encountered several operational and process-based challenges as they grew, which necessitated a robust digital solution:
- Complex Inventory Management: Tracking large volumes of materials and components across different production stages was challenging and often led to delays and inaccuracies.
- Manual Workflow and Production Tracking: H.M.A. relied on manual data entry for production status, which was time-consuming, error-prone, and lacked real-time visibility.
- Limited Data Access and Reporting: Without a centralized system, H.M.A. struggled to gather real-time insights into production timelines, resource utilization, and equipment status, impacting decision-making.
- Scalability and Flexibility: H.M.A. needed a solution that could scale with its operations and adapt to future growth in both production volume and product lines.
Consulting Solution
Datazen Technologies developed a custom application tailored specifically to H.M.A.’s industrial manufacturing processes. The solution focused on automating critical workflows, improving data visibility, and integrating inventory and production management functionalities. Key features included:
- Real-Time Inventory Tracking: The application provided a centralized platform for tracking raw materials and finished products in real time, reducing stockouts and overstock situations.
- Automated Production Monitoring: An automated dashboard allowed team members to monitor production stages, track output in real time, and identify potential delays or resource bottlenecks.
- Data Analytics and Reporting Tools: Integrated analytics tools gave managers access to production KPIs, inventory levels, and equipment efficiency, supporting data-driven decisions and strategic planning.
- Scalable Architecture: Built to adapt to H.M.A.’s evolving needs, the application allowed easy integration of additional modules, enabling H.M.A. to scale operations as demand grew.
Implementation
Datazen Technologies took a phased approach to the application development to ensure seamless integration with H.M.A.’s existing processes and tools:
- Phase 1: Requirement Analysis and Application Design - Datazen held a series of discovery workshops with H.M.A.’s operations and IT teams to gather requirements and understand workflows, inventory management needs, and production tracking requirements. Based on these insights, the team designed a modular application framework that could accommodate future expansion.
- Phase 2: Application Development and Testing - Datazen’s development team built a prototype with key features, including inventory and production tracking, data visualization, and automated notifications. After successful testing, the final application was developed, incorporating H.M.A.’s feedback to optimize usability and functionality
- Phase 3: Deployment and Training - Datazen provided a smooth rollout with comprehensive training sessions for H.M.A.’s production, inventory, and management teams. The team also provided ongoing support to ensure rapid issue resolution and tailored modifications based on user feedback.
Results
The custom application provided H.M.A. Enterprises with numerous operational improvements and measurable outcomes:
- Improved Inventory Accuracy: Real-time tracking reduced stock inaccuracies by 35%, minimizing delays and enabling efficient use of materials.
- Enhanced Production Efficiency: Automated tracking and workflow visibility helped reduce production cycle times by 20%, allowing H.M.A. to fulfill orders more quickly and reliably.
- Data-Driven Insights: The application’s analytics tools enabled H.M.A. to make data-backed decisions, optimize resource allocation, and forecast production needs accurately, leading to an estimated 15% increase in output.
- Scalability and Flexibility: Built for future growth, the application allowed H.M.A. to streamline additional processes and manage increasing production volumes with ease.
Datazen Technologies successfully developed a custom application solution that addressed the specific needs of H.M.A. Enterprises’ industrial equipment manufacturing operations. By streamlining inventory and production management and providing actionable insights, the application has equipped H.M.A. with the tools needed to optimize processes, scale with demand, and continue leading in the industrial equipment sector.
Client Feedback
“The application developed by Datazen has been transformative for our manufacturing operations. We now have a seamless, real-time view of our inventory and production workflows. Datazen’s team truly understood our unique requirements and provided a solution that has significantly boosted our efficiency.”
— Operations Manager, H.M.A. Enterprises
Future Plans
Datazen Technologies will continue to support H.M.A. with enhancements to the application, including integration with IoT devices for machine monitoring, advanced production forecasting, and further reporting functionalities. This ongoing partnership aims to support H.M.A.’s growth, ensuring the application evolves in tandem with their needs for efficiency and productivity.
Case Information
Client :
H.M.A. Enterprises
Industry:
Industrial Equipment Manufacturing
Services Provided:
Custom Application Development
Duration:
8 Months